پلاسما اسپری
پلاسما اسپری یکی از روشهای پاشش حرارتی است که امروزه در صنعت بسیار مورد استفاده قرار میگیرد وعلت آن ارزان بودن، سرعت بالای پوشش دهی و کیفیت مناسب پوشش میباشد. این روش عموماً موادی سخت با نقطه ذوب بالا را روی قطعات حساس مانند سوپرآلیاژها مینشانند.
تاریخچه
درسال۱۹۶۰نیاز به پوششهای حرفه ای تر، با گسترش و تنوع مواد، درصنعت احساس شد. دراین بین بود که سیستمهای پلاسما اسپری ساخت و مورد بهرهبرداری قرار گرفت که اولین مشعلهای اسپری پلاسما در سال ۱۹۷۵ساخته شد.[1]
اساس پلاسما اسپری
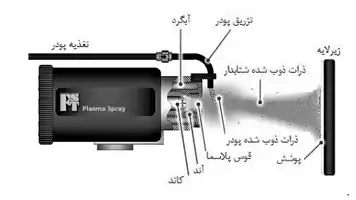
برای برقراری یک پلاسما اسپری پایدار، گاز محیط باید یونیزه گردد. در پاشش پلاسمایی از یک قوس الکتریکی که درتفنگ برقرار میشود، به عنوان منبع گرما استفاده میشود، قوس بین کاتد تولیدکننده الکترون از جنس تنگستن یا اکسید توریم و آندخنک شونده با آب از جنس مس رخ میدهد.
الکترونهای شتاب دار باعث یونیزه شدن گازهایی مانند نیتروژن و آرگون و آزاد شدن الکترون و یونهای مثیت میشوند که هردو در یک میدان الکتریکی شتاب مییابند. در اثر برخورد الکترونهای شتاب دار با اتمها، مجدداً یونیزاسیون انجام میشود و این پدیده مرتب تکرار میشود به طوری که یک توده الکترون تشکیل میگردد. با تزریق گاز و نیز اعمال انرژی الکتریکی بهطور مداوم ومناسب، پلاسما میتواند حفظ شود ودربین الکترودها پایدار بماند.
یونش دردمای بالا
در انرژیهای بالاتر، یونیزاسیون بیشتر از جداشدن شیمیایی رخ میدهد. در یک گاز واکنشی معمولی، از هر صد مولکول، یک رادیکال آزاد تشکیل میشود در حالی که در یونیزاسیون از یک میلیون مولکول یکی یونیزه میشود. تأثیر غالب در این شرایط رادیکالهای آزاد است. اثرات یونی با انتخاب پارامترهای فرایند ودر صورت لزوم استفاده از گازنجیب غالب میشود.[2]
گازهای مورد استفاده پلاسما
نحوه عملکرد گازهای مورد استفاده پلاسما
گاز مورد استفاده در فرایند پوشش دهی پلاسما اسپری معمولاً آرگون است ولی در کنار گاز آرگون عموماً از گازهای دیگری نظیر نیتروژن و هیدروژن نیزبه عنوان گاز ثانویه استفاده میشود. نوع و ترکیب گازهای مورد استفاده در این فرایند بر پایه قابلیت ذوب کردن ذرات پودر است. این قابلیت درمورد گازهای مولکولی (یا اصطلاحاً دو اتمی، مخصوصاً هیدروژن) بسیار بیشتر از گازهای تک اتمی (مثل آرگون) است. مهمترین علت این امر، بالا بودن قابلیت انتقال حرارت در مورد گازهای مولکولی است. از طرف دیگر در جت، گازهای خروجی تک اتمی سرعت بسیار بیشتری از گازهای مولکولی دارند؛ بنابراین با استفاده از مخلوط این گازها به نسبت بهینه میتوان ذوب کامل ذرات پوشش را به همراه سرعت بالای خروجی گاز به دست آورد. (در تأسیسات جدید پلاسما اسپری، جت گاز دارای سرعتی معادل چندین برابر سرعت صوت است).[3]
نحوه ایجاد پوشش از طریق پلاسما اسپری
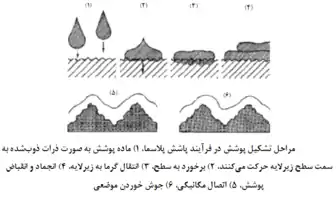
ماده تشکیل دهنده پوشش به صورت پودر با کمک یک گاز حمل کننده به جت پلاسما تزریق میشود. ذرات برحسب اندازه ای که دارند نیمه ذوب یا ذوب شده و به طرف سطح قطعه که از پیش آماده شده رانده میشوند. ذرات در اثر برخورد به سطح، پهن شده و بلافاصله در اثر انتقال گرما به ماده زیر لایه سرد، جامد میگردد. چسبندگی پوشش اساساً با اتصال مکانیکی است و به صورت موضعی بانیروهای اتصال شیمیایی مواد پوشش به زیر لایه تأمین میگردد. برای به دست آوردن چسبندگی قوی در پوشش، سطح تمیز شده و زیرلایه باید توسط ماسه پاشی ناهموار شود. این عمل اتصال خوب مکانیکی را فراهم میکند. دراین روش پارامترهایی نظیر جریان جرم، سرعت مشعل پلاسما و تعداد پاسها ضخامت نهایی پوشش را تأمین میکنند.
فرایندهای گوناگون پلاسما اسپری
- پلاسمااسپری اتمسفری
- پلاسما اسپری در خلاء
پلاسما اسپری اتمسفری
از لحاظ اقتصادی عمومیترین نوع این فرایند است. اسپری پلاسمای اتمسفری در هوا است. ذرات پودر میتوانند با اتمسفر هوا واکنش داشته باشند؛ که این امر باعث محدودیت درانتخاب مواد پاششی میگردد. چون باعث ایجاد مواد اکسیدی درون پوشش میشود. عمدهترین زمینه کاربردهای این روش، ایجاد پوشش مقاوم به سایش، خوردگی (سیال، گاز) و سد حرارتی برپایهٔ مواد سرامیکی اکسیدی است. مواد پوشش معمول دیگر شامل فلزات و برخی آلیاژها به خصوص آلیاژهای غیر حساس به اکسایش است. اما با توجه به کیفیت پوشش وهزینه پوشش دهی کمتراین فرایند، برای مواد سرامیکی غیر اکسیدی در صنعت کاربرد گستردهای پیدا کرد. تخلخل پوششهای پلاسما اسپری در اتمسفرمحیط ۱ تا ۵ درصد است. فاصله پاشش بین زیر لایه و مشعل پلاسما ۱۰۰ تا ۱۵۰ میلیمتر است که بستگی به نوع ماده و پارامترهای پاشش دارد.
عیب این روش: ریز ساختار حاصل معمولاً شامل تعداد زیادی از ریز ترکها، حفرات و آخالهاست. معایب موجود درپوشش باعث میشوند که امکان نفوذ جریانهای مذاب فلزات یا نمکهای مذاب موجود در محیط فراهم شده و امکان خوردگی پوشش اتصال و در نهایت شکست و تخریب قطعه فراهم شود.
پلاسما اسپری در خلاء
این فرایند در یک اتاقک با فشار کاهش یافته انجام میپذیرد. فرایند پوشش دهی پس از تخلیه اتاقک تافشار کمتر از ۰٫۱ میلی بار و پر کردن آن با یک گاز خنثی با فشار ۵۰ تا ۴۰۰ میلی بار آغاز میگردد. در این روش امکان پاک کردن سطح زیر لایه مخصوصاً از لایههای اکسیدی وجود دارد و نیز زیرلایه را پیش گرم میتوان کرد که هردوعامل باعث چسبندگی بهتر میگردند. دمای زیرلایه در این روش خیلی بالا میرود زیرا امکان خنک شدن زیرلایه از طریق همرفت به دلیل افت فشار اتاقک کاهش مییابد. اگرچه دمای بالای ذرات باعث بهتر شدن استحکام جسبندگی پوشش میگردد چون در این حالت نفوذ افزایش یافته و تنشهای ناشی ازخنک کاری کاهش پیدا میکند؛ ولی باید مدنظر داشت که دمای زیر لایه ازمقدار بحرانی افزایش پیدا نکند.
فاصله پاشش در این فرایند معولا بین ۲۵۰ تا۳۰۰ میلیمتر است و تخلخل پوششهای حاصله کمتر از ۱ درصد است و ضخامت پوششها معمولاً بین ۱۰۰ تا ۱۵۰ میکرومتر است. کاهش فشار اتاقک تا حدود ۰٫۱ میلی بار باعث میگردد تا بخش عمدهٔ اکسیژن از اتاقک خارج گردد در نتیجه امکان استفاده از مواد حساس به اکسایش هم در زیرلایه وهم در ماده پوشش فراهم میگردد.
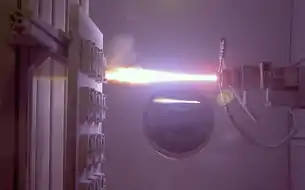
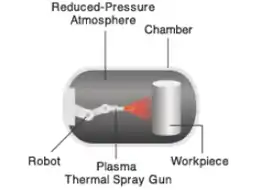
کاربردها
مزایا
- دمای بالای شعله ایجاد شده، پوشش دادن مواد دیرگداز و مواد بانقطه ذوب بالا را ممکن میسازد.
- محدوده وسیعی از مواد قابل پوشش هستند.
- کیفیت پوشش درمقایسه با سایر روشهای پوشش دهی بهتر است.
- ذرات با توزیع اندازه بین ۲۰تا۱۵۰ میکرون برای پوشش دادن قابل استفاده است.
- تخلخل پوششهای حاصله را میتوان با کنترل فرایند به زیر۱٪ رساند.
- میتوان پوششهایی با ضخامت ۰٫۰۷تا چند میلیمتر راایجاد کرد.
- قدرت و استحکام چسبندگی از ۱۷مگا پاسکال در آلیاژهای نرم تا۸۳ مگاپاسکال در پوششهای کاربیدی میباشد.
- مقدار اکسید به وجود آمده در پوششهای فلزی بسیار کمتر از سایر روشهای پوشش دهی است.
منابع
- «متال اسپری-پلاسما اسپری-بابیت ریزی-یاتاقان سازی-جوشکاری زیر پودری-جایگاههای سی ان جی». حامین صدرا | متال اسپری | یاتاقان سازی و بابیت ریزی. دریافتشده در ۲۰۱۹-۱۲-۳۱.
- "Thermal spraying". Wikipedia. 2019-12-26.
- poudrafshan. «web».
- «متال اسپری-پلاسما اسپری-بابیت ریزی-یاتاقان سازی-جوشکاری زیر پودری-جایگاههای سی ان جی». حامین صدرا | متال اسپری | یاتاقان سازی و بابیت ریزی. دریافتشده در ۲۰۱۹-۱۲-۳۱.
- فیروزبخت، علیرضا (۱۳۹۳). ایجاد پوشش فروتیک از کنسانتره ایلمنت به روش پلاسما اسپری. پایاننامه کارشناسی ارشد. پژوهشگاه علوم و تحقیقات
- ابراهیمی، حسن (1388).plasma spray coating. کارشناسی ارشد. دانشگاه امیرکبیر
- کمالی، زهرا (۱۳۹۶). بررسی و مقایسه رفتاراکسیداسیون و خوردگی داغ پوششهای سدحرارتی کامپوزیتی زیرکونیای پایدار شده با ایتریا و سریا. پایاننامه کارشناسی ارشد. دانشگاه شهر کرد