شکلدهی الکترومغناطیسی
فرایند شکلدهی الکترومغناطیسی
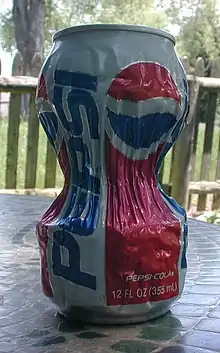
شکلدهی الکترومغناطیسی (به انگلیسی: Electromagnetic forming) یکی از فرایندهای شکلدهی با سرعت بالا[1] است که برای شکلدهی، اتصال، جوشکاری و برش فلزات استفاده میشود. این فرایند یکی از روشهای شکلدهی غیر تماسی است که در آن با کمک میدانهای مغناطیسی پالسی و در نتیجه ایجاد نیروی لورنتس میتوان عمل شکلدهی را انجام داد. اگرچه این فرایند بیشتر برای شکلدهی مواد با هدایت الکتریکی بالا از جمله مس و آلمینیوم رایج است اما میتوان با استفاده از درایورهایی با هدایت الکتریکی بالا، مواد با هدایت الکتریکی پایین از جمله فولادها را نیز شکلدهی نمود[2].

اصول شکلدهی الکترومغناطیسی
در این روش بسته به نوع هندسه قطعه، ابتدا قطعهکار درون، بیرون و یا در مجاورت سیمپیچ قرارمیگیرد. سپس یک منبع تغذیه که به صورت موازی به یک بانک خازنی متصل است ولتاژ شارژ بالایی را به آن اعمال میکند. زمانی که شارژ کامل میشود یک کلید مخصوص توان پالسی نظیر ایگنیترون یا شکاف تخلیه انرژی الکتریکی ذخیره شده را از طریق سیمپیچ راه اندازی میکند. در نتیجه عبور جریان یک میدان مغناطیسی متغیر با زمان با شدت بالا درون سیمپیچ ایجاد میشود که یک جریان گردابی را درون قطعه کار هادی جریان القا میکند. در اثر القای جریان درون قطعهکار یک میدان مغناطیسی دیگر درون قطعه کار حاصل میشود. در اثر تقابل دو میدان مغناطیسی تولید شده، یک نیروی دافعه بین سیمپیچ و قطعه کار به وجود آمده که باعث تغییرفرم دائمی قطعهکار میشود. از آنجا که این نیرو به سیمپیچ نیز وارد میشود، سیمپیچ و عایق روی آن باید از مقاومت خوبی برخوردار باشند تا آسیب نبینند.
طبقه بندی انواع حالات شکلدهی الکترومغناطیسی
اگرچه مبنای به کار گرفته شده در تمامی روشهای این فرایند یکسان است اما بسته به شکلهای متفاوت سیمپیچ و هادی فلزی و نحوه قراگرفتن آن حالتهای مختلفی از آن را میتوان متصور بود. تمامی حالتهای شکلدهی الکترومغناطیسی را میتوان به سه دسته کلی تقسیم کرد[3]:
- متراکمسازی حالت استوانهای: در این روش قطعاتی شبیه به لولههای استوانهای درون سیمپیچهایی به همین شکل قرار گرفته سپس با اعمال فشار از طرف سیمپیچ به قطعهکار، قطر قطعه کاهش مییابد.
- انبساط سازی حالت استوانهای: در این حالت سیمپیچ درون قطعهکار استوانهای قرار گرفته با اعمال فشار از طرف سیمپیچ قطعه کار منبسط میشود. با توجه به شکل هندسی قطعهکار طراحی سیمپیچ در این حالت با محدودیتهایی روبرو میشود.
- شکلدهی ورقهای فلزی: یک سیم پیچ مسطح مارپیچی که در بالا یا پایین ورقه مسطح فلزی قرار گرفتهاست، با اعمال پالس جریان، به جسم نیرو وارد کرده و بعد از سرعت گرفتن و برخورد آن به قالب شکل نهایی قطعهکار بدست میآید.
سیمپیچ
طراحی یک سیمپیچ مناسب یکی از مهمترین مسائل در سیستم شکلدهی الکترومغناطیسی است. از آنجا که سیمپیچ یک عنصر اصلی در ایجاد میدان مغناطیسی مناسب در سیستم است (که منجر به فشار مغناطیسی میشود)، در طراحی آن، برخورداری از استحکام و توانایی انتقال جریان بالا بسیار مهم میباشد. همچنین با توجه به ظرفیت خازنی سیستم، میزان خودالقایی در مقابل مقاومت داخلی آن مهم است. با توجه به این نکته، در سیمپیچهای مارپیچی با افزایش تعداد حلقه (که باعث افزایش خودالقایی میشود) طول سیمپیچ زیاد میشود که نتیجه آن افزایش مقاومت الکتریکی سیمپیچ میباشد. علاوه برخواص الکتریکی سیمپیچ، طراحی ویژگیهای هندسی آن نیز مهم است. بهطور کلی، استفاده ازسیمپیچهای استوانهای در فرایند متراکمسازی و انبساط لولهها بیشتر به کار میروند، اما درشکلدهی ورقهای فلزی تخت از سیمپیچهای تخت مارپیچی استفاده میشود.
سیمپیچ تک حلقه
سادهترین راه برای ایجاد یک سیمپیچ، ماشینکاری یک صفحه هادی جریان است، به این صورت که میتوان با ایجاد یک سوراخ و یک شکاف سیمپیچ سادهای تولید کرد. مواد با هدایت الکتریکی و استحکام تسلیم بالا مانند آلیاژهای آلومینیوم با استحکام بالا، آلیاژهای برلیوم- مس، برنج و مواد مستحکم شده کاندیدهای مناسبی برای ساخت سیمپیچ میباشند. همچنین از روکشهای پلیآمید میتوان برای عایق بندی استفاده کرد. سیمپیچهای تک حلقه میتواند فشار زیادی ایجاد کند، اما آنها اغلب بهدلیل خودالقائی بسیار کمی که دارند، ناکارآمد هستند[4].
سیمپیچهای چند حلقه
سیمپیچ چندحلقه توسط حلقه پیچکردن یک سیم رسانا ساخته میشود. معمولاً از سیمهای مسی برای ساخت این نوع سیمپیچها استفاده میشود. بهطور معمول، سه نوع سیمپیچ تولید میشود: سیمپیچ استوانهای برای متراکمسازی لوله، سیمپیچ استوانهای برای انبساط لوله و سیمپیچ مارپیچی تخت برای شکلدهی ورقها
شکلدهنده میدان
بهطور کلی، بالاترین فشار الکترومغناطیسی را زمانی میتوان ایجاد کرد که سطح سیمپیچ از یک بلوک فلزی یکپارچه با استحکام بالا (و رسانایی بالا) ساخته شده باشند. از این رو، فشارهای زیاد اغلب میتوانند با سیمپیچهای تک حلقه ایجاد شوند. برای ایجاد فشار الکترومغناطیسی بالا میتوان از سیمپیچهای شامل شکلدهنده میدان استفاده کرد همچنین شکلدهنده میدان قادر به افزایش و تنظیم خودالقایی سیمپیچ نیز میباشد[4]. از شکلدهنده میدان برای متمرکز کردن شار مغناطیسی و تولید فشار مغناطیسی بر روی منطقه مورد نظر از قطعهکار استفاده میشود. شکلدهنده میدان انرژی تولید شده توسط سیمپیچ را به مناطق خاص هدایت میکند[5].
کاربردهای شکلدهی الکترومغناطیسی
امروزه بیشترین کاربرد این فناوری در صنایع خودروسازی، هوافضا میباشد. چرا که مسئله کاهش مصرف سوخت یکی از اهداف تولیدکنندگان است. یکی از راههای رسیدن به این هدف، کاهش وزن سازه میباشد. در همین راستا استفاده از آلومینیوم در صنایع مختلف کاربرد گستردهای پیدا کردهاست، اما مشکلی که در استفاده از این فلز و آلیاژهای آن وجود دارد، قابلیت شکلپذیری و شکلدهی پایین آن و همچنین ایجاد ترک و چروکیدگی در آن بعد از فرمدهی میباشد. اما استفاده از روشهای شکلدهی سرعت بالا نظیر شکلدهی الکترومغناطیسی در شکل دادن به آلومینیوم بسیار موفق عمل کردهاست. در واقع آزمایشهای تجربی نشان میدهد اگر نمونه با سرعت بسیار زیاد تحت فشار قرار گیرد، احتمال ایجاد ترک در آن کمتر است. مهمترین کاربردهای شکلدهی الکترومغناطیسی عبارت اند از:
- همینگ الکترومغناطیسی
- شکلدهی الکترومغناطیسی گرم منیزیم
- کالیبراسیون ورقهای آلمینیومی و فولادی
- کشش عمیق با ترکیب شکلدهی الکترومغناطیسی
- ترکیب نورد و شکلدهی الکترومغناطیسی
مقایسه با سایر فرایندهای شکلدهی مکانیکی
شکلدهی الکترومغناطیسی دارای مزایا و معایبی متعددی نسب به سایر فرایندهای معمول شکلدهی میباشد. برخی از این مزایا عبارت اند از:
- بهبود قابلیت شکلپذیری( افزایش مقدار اعمال کشش به قطعهکار بدون ایجاد پارگی در آن).
- کاهش قابل توجه چروکیدگی در حین شکلدهی.
- امکان شکلدهی، مونتاژ و اتصال با سایر مواد همجنس و غیر همجنس همانند کامپوزیتهای پایه فلزی و سایر فلزات دیگر.
- دستیابی به تلورانسهای دقیق با توجه به کاهش و یا حذف برگشتفنری در طول فرایند.
- استفاده از قالبهای تککفه و در نتیجه کاهش هزینه ابزار
- کاهش و یا حذف روانکار
- عدم وجود نیروهای تماسی و در نتیجه افزایش کیفیت سطح
اصلیترین معایب شکلدهی الکترومغناطیسی عبارت اند از:
- عدم امکان شکلدهی قطعات نارسانای الکتریکی بهصورت مستقیم و نیاز به درایورهای هادی جریان جهت شکلدهی.
- نیاز به ایمنی بالا جهت اعمال ولتاژ و جریان زیاد.
منابع
<P. Gharghabi, et al. “Impact of Metal Thickness and Field-Shaper on the Time-Variant Processes during Impulse Electromagnetic Forming in Tubular Geometries” Journal of the Korean Physical Society, 59(61); p. 3560-3566, 2011.>
- [journals.sagepub.com, Aug 25, 2017 · License: CC BY 4.0 "A study on the high-speed forming press using electromagnetic force"] Check
|پیوند=
value (help). sage (به english). Min Kuk Choi, Chan Gon Park, Young Choi, Ji Yeon Shim and Bong Yong Kang. Date received: 2 February 2017; accepted: 26 May 2017. doi:10.1177/1687814017716074. line feed character in|ناشر=
at position 54 (help); Check date values in:|تاریخ=
(help) - "Effect of an aluminum driver sheet on the electromagnetic forming of DP780 steel sheet". Journal of Materials Processing Technology (به english). Hyeonil Park, Daeyong Kim, Jinwoo Lee, Se-Jong Kim, Youngseon Lee, Young Hoon Moon. 2016.
- S.G Daehn (۲۰۰۶). “High Velocity Metal Forming”, ASM Handbook Volume 14B Sheet Metalworking. ASM International. صص. pp٫ ۴۰۵‐۴۱۸.
- "Effect of fieldshaper on magnetic pressure in
electromagnetic forming". Journal of Materials Processing Technology (به english). ] Haiping Yu, Chunfeng Li, Zhiheng Zhao, Zhong Li: Volume 168, Issue 2,
, Pages 245‐249. 30
September 2005. line feed character in
|عنوان=
at position 46 (help); line feed character in|تاریخ=
at position 3 (help); line feed character in|صفحه=
at position 22 (help); Check date values in:|تاریخ=
(help)