ریختهگری نیمهجامد
ریختهگری نیمه جامد (به انگلیسی: Semi-solid metal casting) نوع دیگری از ریختهگری تحت فشار است.[1] این فرایند برای فلزات غیرآهنی، مانند آلومینیوم، مس،[2] و منیزیم استفاده میشود. این فرایند مزایای ریختهگری و آهنگری را باهم درمیآمیزد. نام این فرایند از یک خاصیت سیال بنام تیکسوتروپی گرفته شدهاست که امکان انجام این فرایند را فراهم میکند. بهطور سادهتر، سیالات تیکسوتروپی زمانیکه ماده جریان مییابد برش داده میشوند اما درحالت ساکن غلیظ تر میشوند.[3] این نوع فرایند برای اولین بار در اوایل دهه[3] ۱۹۷۰ توسط پروفسور فلمینگز در مؤسسه فناوری ماساچوست شناخته شد. چهار فرایند مختلف برای ریختهگری نیمه جامد وجو دارد: تیکسوکستینگ، ریوکستینگ، تیکسومدلینگ و SIMA.
ریختهگری نیمه جامد در یک دمایی که فلز را بین دماهای لیکوئیدوس و سالیدوس قرار میدهد انجام میشود. بهطور ایدهآل، فلز باید ۳۰ تا ۶۶ درصد جامد باشد. فلز باید ویسکوزیته کمی داشته باشد تا قابل استفاده باشد و برای رسیدن به این ویسکوزیته کم ماده نیازمند یک شکل اولیه کروی احاطه شده توسط فاز مذاب است.[2] رنج دمایی امکانپذیر به ماده بستگی دارد و برای آلیاژهای آلومینیوم ۵ تا ۱۰ درجه سانتیگراد است، اما برای آلیاژهای مس با رنج ذوبی باریک میتواند فقط چند دهم درجه باشد.[4]
ریختهگری نیمه جامد معمولاً برای ریختهگریهای high end استفاده میشود. برای قطعات معمولی آلیاژهای آلومینیوم شامل پایههای معلق موتور، ورد سنسوری منیفولد هوا، قالبهای موتور و محفظه فیلتر پمپ نفت.[5]
فرایندها
تکنیکهای مختلفی برای تولید ریختههای نیمه جامد وجود دارد. برای آلیاژهای آلومینیوم فرآیندهای معمول تیکسوکستینگ و ریوکستینگ میباشد.
برای آلیاژهای منیزیم، متداولترین فرایند ملدینگ است.[6]
تیکسوکستینگ
تیکسوکستینگ (به انگلیسی: Thixocasting) در دهه ۱۹۹۰ ایجاد شد.[7] در این روش از یک شمش ریخته شده با یک ساختار غیر دندریتی استفاده میشود بدین صورت که این میله پیش گرم میشود تا به دمای نیمه جامد برسد سپس تزریق میشود.[8] شمش مورد استفاده در این روش معمولاً از هم زدن شدید مذاب هنگام ریختهگری تولید میشود. معمولاً از گرمای القایی برای دوباره گرم کردن شمشها تا رنج دمای نیمه جامد و از ماشینهای دایکست برای تزریق ماده نیمه جامد به داخل دایهای فولادی سخت شدهاستفاده میشود. تیکسوکستینگ در آمریکای شمالی، اروپا و آسیا به صورت تجاری در حال انجام است. تیکسوکستینگ این قابلیت را دارد تا اجزای با کیفیت بسیار بالا را به دلیل سازگاری محصول که از شمش ریختهگری شده تحت شرایط فرآیندهای مداوم ایدهآل مشابهی که برای تولید مواد خام نورد و فروج بکار میروند بدست میآید، تولید کند.[8] از مزایای آن میتوان به توانایی ایجاد سطوح با کیفیت بالا اشاره کرد. اصلیترین عیب این روش این است که به دلیل شمشهای مخصوصی که باید استفاده شود، روش گرانی است. از معایب دیگر میتوان به محدودیت استفاده از آلیاژها اشاره کرد و همچنین موادزائد تولیدی در این روش بهطور مستقیم نمیتوانند دوباره مورد استفاده قرار گیرند.[9][10]
رئوکستینگ
رئوکستینگ (به انگلیسی: Rheocasting) در دهه ۲۰۰۰ به وجود آمد. برخلاف تیکسوکستینگ که یک شمش را دوباره گرم میکند، از دوغاب نیمه جامد بدست آمده از فلز ذوب شده در یک ماشین یا کوره دایکست استفاده میکند.[8] وجود این دوغاب مزایایی دارد که مانند کاهش انقباض و مقدار حرارت مورد استفاده دارد. این یک مزیت نسبت به روش تیکسوکستینگ است زیرا باعث کمتر شدن هزینه مواد اولیه در آلیاژهای دایکست معمول میشود و بازیافت مستقیم را ممکن میسازد.[10][11]
در این روش ابتدا آلیاژ مورد نظر ذوب شده و به مذاب تبدیل میشود، سپس تا رنج دمایی نیمه جامد پائین آورده میشود.
یک روش ریوکستینگ استفاده شده در صنعت، تکنولوژی به اصطلاح “تغییرشکل سریع دوغاب” است که توسط مگنوس وسن و هایپینگ کاوو اختراع شدهاست. در این تکنولوژی فلز مذاب توسط چرخش یک قطعه جامد آلومینیومی درون آن سرد میشود. نیروی برشی چرخنده دندریتها را برش میدهد و منجر به ساختار کریستالی گرد میشود که باعث تنش کمتر در ماشینکاری و پر کردن بهتر قالب میشود.
به دلیل حرکت دوغاب و سیلان خیلی خوب در ساختار کروی و ویسکوزیته کمتر آن نسبت به حالت دندریتی، در مرحله قبل از تزریق نیمه جامد به داخل قالب، دوغاب را به وسیله ایجاد تنش برشی از ساختار دندریتی به ساختار گلولهای تبدیل میکنیم. در اثر ایجاد تنش برشی، دندریتها خم میشوند و دولبه آنها به هم میرسند و درون آنها مقداری مذاب محبوس میشود. دندریتهای چاق، چاق تر میشوند و دندریتهای لاغر مجاور خود را در خود حل میکنند. این کار تا جائی ادامه مییابد که ساختار بهطور کامل کروی شود. پارامترهای مؤثر بر غیردندریتی شدن در فرایند رئوکستینگ عبارتند از:
نرخ برش
درمجموع هرچه نرخ برش بیشتر باشد، مذاب حبس شده در جامد کاهش مییابد.
سرعت سردکردن (انجماد)
هرچه سرعت سردکردن (انجماد) کاهش مییابد و به سمت ساختار گلبولی میرود، مذاب حبس شده در جامد کمتر میشود.
زمان انجماد
زمان انجماد هرچه بیشتر باشد، به ساختار گلبولی نزدیکتر شویم زیرا زمان انجماد و سرعت انجماد با هم رابطه عکس دارند و با گذشت زمان ویسکوزیته کاهش مییابد.
بچ ریوکستر
در روش بچ ریوکستر (به انگلیسی: Batch Rheocaster) داخل یک دیگ پر از دوغاب دندریتی میشود. سپس به وسیلهٔ دو بازوی مکانیکی خودکار، شروع به ایجاد تلاطم وتنش برشی درنیمه جامد میکنند تا ساختار کروی و گلبوله شود. این روش به علت ارزان بودن آن تقریباً به عنوان رایجترین روش محسوب میشود.
ریوکستر پیوسته
در روش ریوکستر پیوسته (به انگلیسی: Continous Rheocaster) دوغاب با ساختار دندریتی از بالا وارد میشود. درون دستگاه اهرمی وجود دارد که علاوه بر حرکت دورانی، حرکت ارتعاشی از بالا به پایین هم دارد. این حرکت باعث میشود که در پایین دستگاه و جاهایی که قطر مخزن کم میشود ساختار به صورت گلبوله درآید و از خروجی پایین دستگاه خارج شود. مزیت این روش نسبت به روش قبل این است که عملیات به صورت پیوسته انجام میشود و تا زمانیکه از بالا نیمه جامد با ساختار دندریتی وارد میشود، ازپایین میتوانیم ساختار گلبولهای بدست آوریم؛ لذاسرعت این روش برعکس روش قبل بسیار بالاست.
ریوکستر پیوسته با همزن الکترومغناطیسی
این روش (به انگلیسی: Electromegnatic Stirring of Continous Casting) امروزه به علت مزیتی که نسبت به دو روش قبلی دارد از اهیمت بسیار بالایی برخوردار است. در دو روش قبلی، تبدیل ساختار دندریتی به ساختار گلبوله توسط یک عامل مکانیکی صورت میگرفت (بازوهای اعمال تنش برشی)؛ لذا باید جنس این بازوها طوری باشد که دمای ذوب بالاتر از دوغاب داشته باشند. اما در ریوکستر پیوسته با همزن الکترومغناطیسی، عامل مکانیکی وجود ندارد و تبدیل ساختارها به وسیله یک نیروی الکترومغناطیسی صورت میگیرد.
در نتیجه برای نیمه جامدها و آلیاژها با دمای ذوب بالا (مانند فولادها) این روش بسیار کاربرد دارد. شمشهای مورد استفاده برای تیکسوکستینگ از این روش تولید میشوند. در این روش نیز عملیات به صورت پیوسته و مداوم است.
مگنتو هیدرودینامیکی
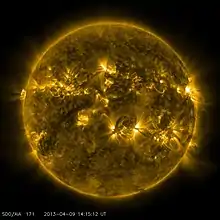
مگنتو هیدرودینامیکی (به انگلیسی: Magneto Hydrodynamic یا به اختصار MHD) عبارت است از ایجاد تلاطم شدید و خشن در هسته کوره القائی که موجب میشود ساختار به صورت گلبوله در آید. این روش برای ضخامتهای زیاد بکار میرود.[12] خورشید یک سیستم مگنو هیدرودینامیکی است که به خوبی شناخته نشدهاست.
تیکسومولدینگ
تیکسومولدینگ (به انگلیسی: Thixomolding) همان روش تزریق منیزیم هست که روش مناسبی برای تولید موادی سبکتر و محکمتر از آلومینیوم است.[13] برای آلیاژهای منیزیم، تیکسومولدینگ از یک ماشین مشابه تزریق قالب استفاده میکند. در یک فرایند تک مرحلهای، تکههایی از آلیاژ منیزیم در محفظهای تحت گاز آرگون تا دمای ۴۰ درجه سانتی گراد گرم میشود. وجود گاز آرگون برای جلوگیری از اکسید شدن منیزیم است. دمای ۴۰ درجه میتوان دمای نیمه جامد منیزیم نامید. یک فیدر پیچی قرارداده شده درون محفظه تکههای منیزیم را همزمان با گرم شدن تا بازه دمایی نیمه جامد کنترل میکند. سپس حالت نیمه جامد منیزیم مانند روش دایکست تحت فشار نسبتاً بالایی به درون حفرههای قالب رانده میشود. چرخش پیچ نیروی برشی لازم برای تولید ساختار کروی ریختهگری نیمه جامد را فراهم میکند. زمانیکه دوغاب به اندازه موردنیاز فراهم شد، پیچ در داخل قالب فولادی برای تزریق دوغاب به جلو حرکت میکند.[14] در این روش بر عکس روش ریختهگری جریان مواد آشفته نیست و آرام است. به همین خاطر مذاب تحت خلأ نگهداری میشود که برای طراحی قطعات پیچیده بسیار مؤثر است.
در این روش احتمال تخلخل نسبت به دایکست کمتر است. همچنین در این روش درگاهها و راههای ارتباطی بین قطعات در قالب همانند قطعات منیزیم ۱۰۰ درصد قابل بازیافت هستند. علاوه بر بازیافت پذیری، این روش فواید زیستمحیطی، اقتصادی و عملکردی نیز دارد؛ در این روش مذاب اضافی وجود ندارد. هم چنین ماده تهنشین شونده، کم کیفیت یا دور ریز نیز وجود ندارد. همچنین دمای کاری ۱۳۰ درجه سانتی گراد است که از دمای کاری در دایکست کمتر است. کم بودن دمای کاری باعث افزایش عمر کاری تجهیزات میشود.[15] هم چنین باعث کمتر شدن حرارت مورد استفاده نیز میگردد.
SIMA
در این روش ماده ابتدا تا دمای ریختهگری نیمه جامد گرم میشود. هنگامیکه به دمای سالیدوس نزدیک میشود، دانهها تبلور مجدد میشوند تا یک ساختار با دانه بندی خوب را تشکیل دهند. بعد از اینکه از دمای سالیدوس رد شد، مرزهای دانهها برای تشکیل ریز ساختار ریختهگری نیمه جامد ذوب میشوند.[2] برای اینکه این روش کار کند، ماده باید در حالت دمایی نیمه سخت اکسترود یا نورد سرد شود. این روش محدود به قطر میله کمتر از ۳۷ میلیمتر (۱٫۵ اینچ) میشود. به همین دلیل تنها قطعات کوچکتر میتوانند ریختهگری شوند.
این روش هم مشابه روش MHD است با این تفاوت که کاربرد آن برای ضخامتهای نازک (در حد کمتر از چند سانتیمتر) میباشد.[12][16]
مزایا
مزایای کلی ریختهگری نیمه جامد عبارتست از:[17]
- تولید قطعات پیچیده
- عاری از تخلخل
- انقباض کاهش یافته
- عملکرد مکانیکی عالی
- کم بودن فشار
- تلورانسهای کم
- دیوارههای نازک
- قابلیت عملیات حرارتی
به دلیل پرشدن آرام محفظهٔ قالب و دمای پایین در فرایند نیمه جامد مزایای زیادی برای قطعات تولید شده به روش نیمه جامد در مقایسه با فرآیندهای شکلدهی معمولی وجود دارد.
- محتوای گرمایی کمتر نسبت به فلز مذاب:
- سایش کمتر قالب
- شکلدهی مواد فعال
- شکلدهی آلیاژهای پایهٔ آهن
- شکلدهی مواد با نقطه ذوب بالا
- حضور فاز جامد در هنگام پرشدن قالب:
- حفرات انقباضی کمتر
- نیاز به تغذیه کمتر
- جدایش کمتر
- ساختار با دانههای کوچکتر
- ویسکوزیتهٔ بالاتر از فلزات مذاب و قابل کنترل:
- گازهای گیر افتادهٔ کمتر
- اکسیدهای کمتر
- شکلدهی باسرعت بالاتر
- کیفیت سطحی بالاتر
- اتوماسیون
- فرآیندهای جدید
- تنش سیلان کمتر از فلزات جامد:
- شکلدهی اجزای پیچیده
- شکلدهی باسرعت بالاتر
- قیمت پایینتر
- شکلدهی باسرعت بالای اجزا به صورت پیوسته
- قابلیت وارد نمودن مواد جدید که منجر به تولید کامپوزیتها میشود
- توانایی جدانمودن مذاب و جامد و خالص سازی[12]
به دلیل فشارها و دماهای پایین لازم برای دایکست فلز نیمه جامد، ماده دای نیازی به خاص بودن ندارد. گاهی گرافیت یا فولاد زنگ نزن نرمتر ممکن است استفاده شود. حتی دایهای غیر آهنی میتواند برای یکبار استفاده شوند. به همین دلیل، فرایند میتواند برای نیازهای نمونه سازی سریع و تولیدات انبوه مورد استفاده قرارگیرد. همچنین امکان ریختهگری فلزات با نقطه ذوب بالا مانند فولادابزار و استلیت را درصورتیکه یک ماده دای دما بالاتراستفاده شود، میدهد. مزایای دیگر شامل: مکانیزه کردن آسان، پایداری، سرعت تولید برابر یا بهتر از سرعتهای دایکست، بدون حبس هوا، سرعت انقباض کم، و یک ساختار یکنواخت است.[3]
معایب
به دلیل اینکه تیکسوتروپی (حالت نیمه جامد) یک حالت میانی فیزیکی یا رئولوژیکی است، تشکیل یک باند بسیار نازکی تحت شرایط فرایند را حتی در اختلاف دماهای محیطی باید در نظر داشت؛ بنابراین امکانات تولیدی به یک تکنولوژی بالایی نیازمند است و اپراتورها باید دانش و مهارتهای لازم را داشته باشند.
جستارهای وابسته
منابع
- [diecasting.org ""Welcome to MyNADCA!""] Check
|نشانی=
value (help). 2015-08-20. - Young, p. 1.
- «Thixoforming». ۲۰۰۲-۰۴-۲۴. دریافتشده در ۲۰۱۷-۰۴-۰۱.
- Vinarcik, Edward J. (2002-10-16). High Integrity Die Casting Processes. John Wiley & Sons. ISBN 9780471275466.
- P. Kapranos, Proc. 10th Inter. Conf. Semi-Solid Processing of Alloys and Composites, Aachen, Germany & Liege, Belgium, 2008
- S. LeBeau & R Decker, "Microstructural Design of Thixomolded Magnesium Alloys", Proc. 5th Inter. Conf. Semi-Solid Processing of Alloys and Composites, Golden, Colorado, 1998
- "Foundrymag". Retrieved 2017-03-27.
- Stephen P. Midson, Semi-Solid Casting of Aluminum Alloys: An Update, Die Casting Engineer, Sept. 2008.
- «John L. , Jorstad (September 2006), "Aluminum Future Technology in Die Casting", Die Casting Engineering: 18–25».
- "WebCite query result". Retrieved 2017-04-01.
- «Total Materia Blog». دریافتشده در ۲۰۱۷-۰۳-۲۷.
- «مجله علمی آموزشی magsci». بایگانیشده از اصلی در ۳۰ مه ۲۰۱۸. دریافتشده در ۲۰۱۷-۰۳-۲۷.
- "Phillips-Medisize Corporation - Injection Molding & Contract Manufacturing of Metal & Plastic". Retrieved 2017-03-27.
- Stephen P. Midson, Robert K. Kilbert, Stephen E. Le Beau & Raymond Decker, "Guidelines for Producing Magnesium Thixomolded Semi-Solid Components used in Structural Applications", Proc. 8th Inter. Conf. Semi-Solid Processing of Alloys and Composites, Limasol, Cyprus, 2004
- "PlasticsToday". Retrieved 2017-03-27.
- Young, p. 2.
- Stephen P. Midson, NADCA Semi-Solid & Squeeze Casting Conference, Rosemont, Illinois, 1996