شکلدهی (فلزکاری)
شکل دهی فلزات یا فرمینگ (به انگلیسی: Forming) شامل گروه بزرگی از فرایندهای ساخت است که در آن از تغییر شکل پلاستیک (خمیری) برای تغییر شکل قطعات فلزی استفاده میشود.[1]
فرایندهای شکل دهی فلزات
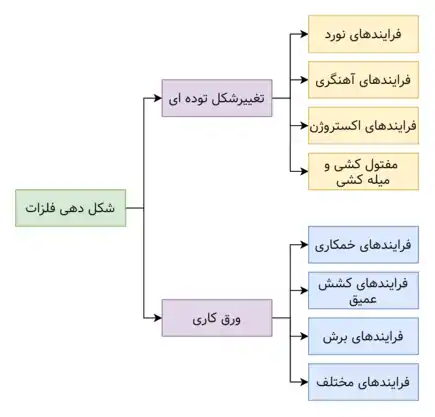
فرایندهای شکل دهی فلزات را میتوان به دو دسته اساسی طبقهبندی کرد: فرایندهای تغییر شکل توده ای و فرایندهای ورق کاری. هر دسته شامل چندین کلاس عمده از عملیاتهای شکل دهی است.
فرایندهای تغییر شکل توده ای
فرایندهای تغییر شکل توده ای بهطور کلی با تغییر شکلهای قابل توجه و تغییرات بزرگ در شکل مشخص میشوند که در آن نسبت سطح-به-حجم کار نسبتاً کوچک است. اصطلاح "توده" قسمتهای کاری را توصیف میکند که دارای این نسبت سطح به حجم کم هستند. اشکال شروع کار برای این فرایندها شامل شمشهای استوانه ای و مستطیلی میشود.
نورد
فرایند نورد یک فرایند تغییر شکل فشاری است که در آن ضخامت یک تختال یا صفحه فلزی توسط دو ابزار استوانه ای مخالف به نام «غلتک» یا «رول» کاهش مییابد. با چرخش غلتکها صفحه به داخل کشیده شده و فشرده میشود.
آهنگری (فورجینگ)
در آهنگری، قطعه کار بین دو قالب مخالف فشرده میشود، به طوری که اشکال روی قالب به روی قطعه کار منتقل میشوند. آهنگری بهطور سنتی یک فرایند کار گرم است، اما امروزه بسیاری از انواع آهنگری به صورت سرد نیز انجام میشود.
اکستروژن
اکستروژن یک فرایند فشرده سازی است که در آن فلز کار به داخل دهانه یک قالب هل داده میشود و در نتیجه شکل مقطع قطعه به شکل سوراخ قالب در میآید.
کشش
در فرایند کشش، قطر یک سیم یا میلگرد با کشیدن آن از درون شکاف یک قالب کاهش مییابد.
فرایندهای ورق کاری
فرایندهای ورق کاری، شامل عملیاتهای شکل دهی و برشکاری است که بر روی ورقها و تسمههای فلزی انجام میشود. در این فرایندها نسبت سطح-به-حجم فلز خام اولیه زیاد است؛ و در نتیجه، این نسبت یک روش مفید برای تشخیص فرایندهای ورق کاری از فرایندهای تغییر شکل توده ای است. از آنجایی که اکثر فرایندهای ورق کاری توسط دستگاههای پرس انجام میشود، معمولاً به آن "پرس کاری" (Pressworking) میگویند. همچنین معمولاً به قطعه ساخته شده توسط یک عملیات ورق کاری، "Stamping" گفته میشود.[1]
عملیات ورق کاری همیشه به صورت فرایند کار سرد و معمولاً با استفاده از مجموعه ای از ابزارها به نام «پانچ» و «قالب» انجام میشود. «پانچ» قسمت مثبت (نری) و «قالب» قسمت منفی (مادگی) مجموعه ابزار است.[1]
خم کاری
خم کاری شامل خم کردن ورق در طول یک خط راست (معمولاً خط راست) برای دادن زاویه ای به آن میشود.
کشش
در ورق کاری، منظور از کشش، تبدیل ورق به شکل یک ظرف تو خالی، از طریق کشیدن آن است. یک ورق گیر (Blankholder) ورق را نگه میدارد تا پانچ آن را بکشد. معمولاً برای تفکیک این عمل از کشش مفتول به آن کشش عمیق میگویند.
برش
در فرایند برش، ورق توسط یک قالب و پانچ برش داده میشود. اگرچه قرار دادن فرایند برش در مجموعه شکل دهی نامربوط به نظر میرسد، اما از آنجایی که اکثر فرایندهای ورق کاری با آن سر و کار دارند در لیست فرایندهای شکل دهی آورده میشود.
متغیرهای شکل دهی فلزات
متغیرهای مستقل
فرایندهای شکلدهی معمولاً سیستمهای پیچیدهای هستند که متشکل از متغیرهای مستقل، متغیرهای وابسته و روابط متقابل وابسته-مستقل هستند. متغیرهای مستقل آن جنبههایی از فرایندی هستند که مهندس یا اپراتور کنترل مستقیمی بر روی آنها دارد و بهطور کلی هنگام تنظیمات اولیه، انتخاب یا مشخص میشوند. برخی از متغیرهای مستقل یک فرایند شکل دهی عبارتند از:[2]
- ماده شروع و اولیه: در هنگام تعیین ماده اولیه، علاوه بر انتخاب ترکیب شیمیایی ماده، وضعیت قبلی آن را نیز انتخاب میکنیم (ریخته شده، بازپخت شده، نورد گرم شده، و…). این متغیرها ممکن است فقط برای سهولت ساخت انتخاب شوند، یا ممکن است با خصوصیات نهایی مورد نیاز پس از اتمام روند تغییر شکل تعیین شوند.
- هندسه اولیه قطعه کار: هندسه شروع ممکن است توسط فراوری قبلی تعیین شده باشد، یا ممکن است از اشکال مختلف موجود انتخاب شود. ملاحظات اقتصادی غالباً در این تصمیم تأثیرگذار است.
- هندسه ابزار یا قالب: این حوزه دارای اهمیت عمده ای است و جنبههای بسیاری دارد، از جمله: قطر و نیمرخ غلتک نورد، شعاع خم در عملیات شکل دهی ورق، زاویه قالب در کشش مفتول یا اکستروژن و جزئیات حفره هنگام آهنگری. از آنجا که ابزار از زمان شروع شکل به محصول نهایی، جریان فلز را القا و کنترل میکند، موفقیت یا عدم موفقیت یک فرایند اغلب به هندسه ابزار بستگی دارد.
- روانکاری: غیرمعمول نیست که اصطکاک بین ابزار و قطعه کار بیش از ۵۰٪ از انرژی تأمین شده برای یک فرایند تغییر شکل را به خود اختصاص دهد. روانکنندهها علاوه بر کاهش اصطکاک، میتوانند به عنوان ماده خنککننده، موانع حرارتی، بازدارندههای خوردگی و ترکیبات جدا کننده نیز عمل کنند. از این رو، انتخاب آنها جنبه مهمی در موفقیت یک عملیات شکل دهی دارد. در مشخصات فنی، نوع روانکننده، مقدار مورد استفاده و روش استفاده آورده میشود.
- دمای شروع: از آنجا که خصوصیات مواد میتوانند با تغییر درجه حرارت تغییر زیادی کنند، انتخاب و کنترل دما اغلب کلید موفقیت یا عدم موفقیت یک عملیات شکل دهی فلز است. دماهای شروع ذکر شده در مشخصات فنی میتواند شامل دماهای قطعه کار و ابزار باشد.
- سرعت عملیات: سرعت کار بسیاری از دستگاههای شکل دهی فلزات را میتوان تغییر داد. از آنجا که سرعت میتواند بهطور مستقیم بر نیروهای مورد نیاز برای تغییر شکل، اثربخشی روانکننده و زمان موجود برای انتقال گرما اثر بگذارد، انتخاب آن فراتر از تأثیر بر نرخ تولید است.
- میزان تغییر شکل: اگرچه برخی از فرایندها این متغیر را از طریق طراحی ابزار کنترل میکنند، اما ممکن است برخی دیگر مانند نورد، اجازه تنظیم آن را به اپراتور نیز بدهند.
متغیرهای وابسته
پس از مشخص شدن متغیرهای مستقل، فرایند سپس ماهیت و مقادیر مجموعه دوم ویژگیهایی را که به عنوان متغیرهای وابسته شناخته میشوند، تعیین میکند، که در اصل، پیامدهای انتخاب متغیر مستقل است. نمونههایی از متغیرهای وابسته شامل موارد زیر است:[2]
- نیرو یا الزامات توان: برای تبدیل ماده انتخابی از شکل اولیه به شکل نهایی، با روانکننده مشخص، هندسه ابزار، سرعت و دمای شروع، مقدار مشخصی نیرو یا توان لازم است. تغییر در هر یک از متغیرهای مستقل منجر به تغییر در نیرو یا توان مورد نیاز خواهد شد، اما تأثیر آن غیر مستقیم است. ما نمیتوانیم مستقیماً نیرو یا توان را مشخص کنیم. ما فقط میتوانیم متغیرهای مستقل را مشخص کنیم و سپس عواقب آن انتخاب را تجربه کنیم. با این وجود بسیار مهم است که بتوانیم نیروها یا توانی را که برای هرگونه عملیات شکل دهی مورد نیاز است پیشبینی کنیم. بدون برآورد منطقی، نمیتوانیم تجهیزات لازم برای فرایند را تعیین کنیم، ابزار مناسب یا مواد قالب را انتخاب کنیم، طرحهای مختلف قالب یا روش تغییر شکل را مقایسه کنیم یا در نهایت فرایند را بهینه کنیم.
- خواص ماده محصول: اگرچه میتوانیم به راحتی خصوصیات ماده اولیه را مشخص کنیم، اما اثرات ترکیبی تغییر شکل و دمای تجربه شده در هنگام شکلگیری، مطمئناً آنها را تغییر میدهد. خصوصیات اولیه مواد ممکن است مورد توجه سازنده باشد، اما مشتری بیشتر به دنبال دریافت شکل نهایی مطلوب با خواص نهایی مطلوب است؛ بنابراین مهم است که بدانیم چگونه خصوصیات اولیه توسط فرایند تولید شکل تغییر میکنند.
- دمای خروج (یا نهایی): تغییر شکل در داخل مواد گرما ایجاد میکند. قطعه کارهای گرم هنگام تماس با ابزارهای سرد، خنک میشوند. روانکنندهها میتوانند ویسکوزیته را تغییر دهند، در صورت گرم شدن بیش از حد تجزیه شوند یا با قطعه کار واکنش نشان دهند. خصوصیات یک ماده مهندسی توسط جنبههای مکانیکی و حرارتی یک فرایند تغییر شکل، تغییر میکند؛ بنابراین، اگر میخواهیم محصولات با کیفیت تولید کنیم، مهم است که درجه حرارت مواد را در طول تغییر شکل کنترل کنیم. (توجه: این واقعیت که دما ممکن است از مکانی به مکان دیگر در محصول متفاوت باشد، بر پیچیدگی این متغیر میافزاید)
- پرداخت سطح و دقت: پرداخت سطح و دقت ابعادی محصول حاصل به جزئیات خاص فرایند شکل دهی بستگی دارد.
- طبیعت جریان ماده: در فرایندهای تغییر شکل، قالبها یا ابزارها، حرکت سطوح خارجی قطعه کار را کنترل میکنند. اگرچه هدف از یک عملیات، تولید یک شکل دلخواه است، اما جریان داخلی مواد ممکن است از اهمیت یکسانی برخوردار باشد. تولید یک محصول بدون نقص با شکل دلخواه و خصوصیات مورد نظر، نیاز به توجه و کنترل تمام جنبههای جریان مواد دارد.
- ناهمسانگردی (Anisotropy) و تنشهای پسماند: بهطور کلی به دلیل جریان مواد، محصولات تولیدی توسط فرایندهای تغییر شکل ناهمسانگردی دارند - به عبارتی ساختار و خصوصیات آن در طول قطعه متغیر است. علاوه بر این، اختلاف در تغییر شکل و تاریخچه حرارتی تمایل به ایجاد تنشهای باقیمانده پیچیده دارد. ناهمسانگردی جهت دار و تنشهای باقیمانده میتوانند مفید یا مضر باشند و باید در تمام محصولات شکل دهی در نظر گرفته شوند.
مدلسازی فرایند

شبیهسازیهای شکل دهی فلز با استفاده از روش مدلسازی المان محدود در دهه ۱۹۸۰ معمول شد اما بهطور کلی به مینی کامپیوترهای قدرت بالا یا ایستگاههای کاری مهندسی نیاز داشت. در اواسط دهه ۱۹۹۰، افزایش سریع قدرت محاسبات امکان مدلسازی فرایندهای پیچیده را در رایانههای شخصی رومیزی فراهم کرد. امروزه با گسترش مداوم قدرت و سرعت محاسبات، شبیهسازی فرایند با سرعتی زیاد، ارزان و کاملاً دقیق انجام میشود. در نتیجه، مدلسازی در همه زمینههای تولید از جمله طراحی قطعه، طراحی فرایند تولید، عملیات حرارتی و بهینهسازی سطح و سایر موارد در حال استفاده است. مدلها میتوانند پیشبینی کنند که چگونه ماده ای به یک فرایند نورد پاسخ میدهد، یک قالب آهنگری را پر میکند، از یک قالب اکستروژن عبور میکند یا در یک قالب ریخته میشود. بارهای موجود در تجهیزات و ابزار را میتوان پیشبینی کرد و میتوان از نقص جلوگیری کرد. مدلهای داغ شکلگیری میتوانند اثرات دما و تغییر دما را که به دلیل انتقال گرما به محیط و ابزار ایجاد میشود، پیشبینی کنند. مدلهای کار سرد میتوانند اثرات سخت شدن کرنشی را محاسبه کنند. کل عملیات حرارتی را میتوان شبیهسازی کرد، از جمله میزان خنک سازی انجام شده توسط مایع خنککننده. مدلها حتی میتوانند توزیع کرنش، تنشهای باقیمانده، ریزساختار و خصوصیات نهایی را در همه نقاط یک محصول پیشبینی کنند.[2]
تکنیکهای پیشرفته شبیهسازی میتوانند درک صحیح و کاملی از یک فرایند ارائه دهند و چرخههای پرهزینه سعی و خطا را حذف کنند. مدلسازی میتواند طراحی و روش تولید محصول را برای افزایش کیفیت و قابلیت اطمینان بهینه کند، در حالی که هزینههای تولید را کاهش میدهد و زمان تحویل را به حداقل میرساند. اگر این مدلها با سنسورهای مناسب ترکیب شوند، میتوان تنظیمات مورد نیاز کنترل بی درنگ فرایند را بدست آورد. مدلهای فرایندی همچنین میتوانند به عنوان ابزار آزمایشگاهی برای کشف ایدههای جدید یا محصولات جدید عمل کنند. کارمندان جدید میتوانند با روشی سریع و ارزان با آنچه جواب میدهد و آنچه جواب نمیدهد، آشنا شوند.[2]
روانکاری
خرابی سطح یا سایش پدیده ای است که با اصطکاک ارتباط مستقیم دارد. از آنجا که قطعه کار فقط در حین کار فرم دهی خود با ابزار ارتباط برقرار میکند، سایشی که قطعه کار تجربه میکند معمولاً ایراد نیست. در واقع، سطح براق و فلز تازه حاصل از سایش اغلب مطلوب است. سایش در ابزار اما کاملاً معکوس است. ابزار شکل دهی معمولاً گران است و انتظار میرود با حفظ مداوم ابعاد خود محصولات بسیاری را شکل دهد. سایش ابزار این ابعاد را تغییر میدهد و بالاخره در زمانی خاص ابزار باید جایگزین شود. از دیگر عواقب سایش ابزار میتوان به افزایش مقاومت اصطکاکی (افزایش توان مورد نیاز و کاهش کارایی فرایند)، پرداخت سطح ضعیف محصول و عدم امکان تولید در هنگام تغییر ابزار اشاره کرد.[2]
روانکاری اغلب کلید موفقیت در عملیات شکل دهی فلزات است. در حالی که روانکنندهها بهطور کلی طبق تواناییشان در کاهش اصطکاک و مهار سایش ابزار انتخاب میشوند، ملاحظات ثانویه ممکن است شامل توانایی عمل به عنوان یک مانع حرارتی (نگه داشتن گرما در قطعه کار و دور از ابزار)، توانایی عمل به عنوان یک ماده خنککننده (از بین بردن گرما از ابزار)، و توانایی جلوگیری از خوردگی در صورت باقی ماندن بر روی محصول تشکیل شده باشد. سایر عوامل تأثیرگذار عبارتند از: سهولت استفاده و حذف. عدم سمی بودن، داشتن بو و اشتعال پذیری. واکنش پذیری یا عدم واکنش با سطوح مواد؛ سازگاری در محدوده مفید فشار، دما و سرعت؛ ویژگیهای خیس کنندگی سطح، هزینه؛ دسترسی؛ و توانایی جریان یافتن یا رقیق شدن و همچنان به عنوان روانکننده عمل کردن. انتخاب روانکار با دانستن این واقعیت که عملکرد روانکار با هر تغییری در شرایط سطح تماس ممکن است تغییر کند، پیچیدهتر میشود. پاسخ دقیق اغلب به عواملی از قبیل پرداخت نهایی هر دو سطح، ناحیه تماس، بار وارد شده، سرعت، دما و مقدار روانکننده بستگی دارد.[2]
توانایی انتخاب روانکننده مناسب میتواند یک عامل حیاتی در تعیین موفقیت یا عدم موفقیت، کارایی یا ناکارآمدی فرایند باشد؛ بنابراین، تلاش قابل توجهی به مطالعه اصطکاک و روانکاری انجام شدهاست، دانشی که به عنوان تریبولوژی شناخته میشود، زیرا هم در شرایط کلی فلزکاری و هم در فرایندهای خاص شکل دهی فلز از آن استفاده میشود.
هزاران ماده شیمیایی روانکننده در دسترس است و بیشتر آنها را میتوان با مواد افزودنی مختلف اصلاح کرد. با این وجود همه آنها را میتوان در انواع مختلفی دستهبندی کرد. روغنهای مستقیم (Straight oils) ترکیباتی با پایه نفتی هستند که به راحتی قابل استفاده هستند و محافظت خوبی در برابر خوردگی دارند اما تمیز کردن آنها دشوار است. روغنهای محلول در آب (امولسیونها) به راحتی تمیز میشوند، اما توان آنها در برابر خوردگی و پایداری طولانی مدت محصول کمتر است. روانکنندههای مصنوعی پایه آب و عاری از نفت هستند. روانکنندههای نیمه سنتتیک ترکیبی از آب، روغنهای پایه نفتی و امولسیون کنندهها (emulsifier) هستند. روانکنندههای لایه-خشک (Dry-film lubricants) اغلب از صابونها یا پلیمرهایی تشکیل شدهاند که به شکل آبی اعمال میشوند و قبل از عمل فرم دهی خشک میشوند. عاملهای پیوند شیمیایی خورده شامل پوششهای اندود شده یا محصولاتی است که در اثر واکنش شیمیایی با قطعه کار تشکیل میشوند.[2]
افزودنیهای فشار شدید یک فیلم شیمیایی تشکیل میدهند که هم به قطعه کار و هم ابزار پیوند میخورند، و باعث افزایش روانکاری تحت فشار و دمای بالا میشوند. مواد افزودنی مرزی (از جمله چربیها و مواد جامدی مانند گرافیت) خود را به سطوح فلزی متصل میکنند و در فشار زیاد، خاصیت ضربهگیری یا جداسازی راحت را فراهم میکنند. سایر افزودنیها میتوانند روانکاری هیدرودینامیکی را بهبود بخشند، در این حالت ترکیب روانکننده و سرعت حرکت نسبی برای ایجاد یک لایه روانکننده ضخیم که از تماس مکانیکی ابزار و قطعه کار جلوگیری کند، کافی است. نیروها و توان مورد نیاز برای عملیات ممکن است ۳۰٪ تا ۴۰٪ کاهش یابد و سایش ابزار کاملاً از بین برود.[2]
ملاحظات دما
در عملیات فلزکاری، دمای قطعه کار میتواند یکی از مهمترین متغیرهای فرایند باشد. بهطور کلی، افزایش دما باعث کاهش استحکام، افزایش شکلپذیری و کاهش میزان سخت شدن کرنشی میشود - همه این اثرات منجر به سهولت تغییر شکل میشود. فرایندهای شکل دهی معمولاً بر اساس دما و ماده ای که در حال شکل دهی است، به فرایند کار در حالت داغ (Hot working)، کار در حالت سرد (Cold Working) و کار در حالت گرم (Warm Working) طبقهبندی میشوند. در کار داغ، تغییر شکل در شرایطی از دما و نرخ کرنش انجام میشود که تبلور مجدد به صورت همزمان با تغییر شکل اتفاق میافتد. برای دستیابی به این هدف، دمای تغییر شکل معمولاً باید بیش از ۰٫۶ برابر نقطه ذوب ماده در مقیاس دمایی مطلق (کلوین یا رانکین) باشد. کار در حالت سرد تغییر شکل در شرایطی است که فرایندهای بازیابی فعال نیستند. در اینجا، دمای کار معمولاً کمتر از ۰٫۳ برابر دمای ذوب قطعه کار است. کار در حالت گرم (Warm Working) تغییر شکل در شرایط گذار است (به عنوان مثال، دمای کاری بین ۰٫۳ تا ۰٫۶ برابر نقطه ذوب).[2]
کار در حالت داغ
کار داغ به عنوان تغییر شکل پلاستیک فلزات در دمای بالاتر از دمای تبلور مجدد تعریف میشود. توجه به این نکته مهم است که دمای تبلور مجدد مواد مختلف بسیار متفاوت است. قلع در دمای اتاق نزدیک به شرایط کار داغ است. فولادها به دمای بیش از ۱۱۰۰ درجه سلسیوس نیاز دارند و تنگستن تا حدود ۲۲۰۰ درجه سلسیوس وارد رژیم کار داغ نمیشود؛ بنابراین، اصطلاح کار داغ لزوماً به هر قطعه داغ و دمایی گفته نمیشود، گرچه معمولاً چنین است.[2]
کار در حالت سرد
تغییر شکل پلاستیکی فلزات زیر دمای تبلور مجدد به عنوان کار سرد شناخته میشود. در اینجا، تغییر شکل معمولاً در دمای اتاق انجام میشود، اما ممکن است از دمای افزایش یافته ملایمی برای افزایش شکلپذیری و کاهش استحکام استفاده شود. از دیدگاه تولید، کار در حالت سرد مزایای قابل توجهی دارد و فرایندهای مختلف کار در حالت سرد کاملاً متداول شدهاست. پیشرفتهای اخیر قابلیتها را گسترش داده و به نظر میرسد روند افزایش کار در حالت سرد ادامه داشته باشد.[2]
در مقایسه با کار در حالت گرم، مزایای کار در حالت سرد شامل موارد زیر است:[2]
- نیازی به گرم کردن قطعه نیست.
- پرداخت سطح آن بهتر است.
- کنترل ابعادی برتری نسبت به کار گرم دارد چرا که ابزار اندازهها را در دمای اتاق ایجاد میکند. در نتیجه، به ماشینکاری ثانویه کمی نیاز است (یا ممکن است هیچ ماشینکاری نیاز نداشته باشد).
- محصولات دارای قابلیت تولید و قابلیت تعویض بهتری هستند.
- استحکام، عمر خستگی و خواص سایشی از طریق سخت شدن کرنشی بهبود مییابد.
- میتوان در قطعه خصوصیات جهت دار ایجاد کرد. (ریز ساختار جهت دار)
- مشکلات آلودگی قطعه به حداقل میرسد.
برخی از معایب مرتبط با فرایندهای کارسرد شامل موارد زیر است:
- برای شروع و تکمیل فرایند تغییر شکل نیروهای بیشتری لازم است.
- تجهیزات سنگین تر و قدرتمندتر و ابزار قوی تری مورد نیاز است.
- شکلپذیری کمتری در دسترس است.
- سطوح فلزی باید کاملاً تمیز و عاری از رسوب باشند.
- ممکن است برای جبران از دست دادن شکلپذیری همراه با سخت شدن کرنشی، به بازپختهای میانی نیاز باشد.
- خصوصیات جهت دار ممکن است مضر باشد.
- ممکن است تنشهای باقیمانده نامطلوب ایجاد شود.